In only seven days, Ideal’s PipeRenew® treatment restores full flow
to 8-in. subsea oil pipeline plugged, with no communication, for ten months.
Offshore, LA | VR-214 Chevron
CUSTOMER CHALLENGE
Paraffin deposition along the entire horizontal length of an 8-in., 7,550-ft subsea oil pipeline was so severe that decommissioning was considered. Four previous attempts to establish communication, by pumping a PAO-100 paraffin inhibitor at more than 1,200 psi, had failed. Prior to losing communication, normal operating pressure was between 75-85 psi. The line was last pigged in 1998.
Deposit analysis indicated a mixture of paraffin wax (17%) and iron oxides (83%). Blockage was identified at 469 ft from the initiation point at one end, and a possible blockage of 467 ft from the initiation point at the other end.
The chart below shows the departing pipeline pressure 14 days prior to
losing communication, as well as the point at which the blockage occurred.
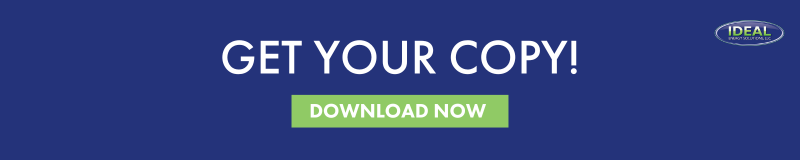
IDEAL'S RESPONSE
Deposit analysis of the plugged material showed the sample contained large amounts of iron oxides. A deposit sample would have to be retrieved from a line with no communication. Based on experience, Ideal personnel thought corrosion material along the pipe wall, combined with the plugged material, caused it to be contaminated and not representative of the actual plug. Ideal believed much higher levels of paraffin and formation materials were present than reported in the deposit analysis.
Ideal recommended their PipeRenew® treatment, the only non-hazardous, environmentally responsible remediation solution that effectively removes paraffin and asphaltenes. The PipeRenew® treatment reacts with the portion of oil that contributes to the acid value to make a simple soap. This breaks up the paraffin and allows it to be pumped out.
Proper pre-job planning, including a site visit, equipment selection, and proposed equipment layout allowed for a safe and effective job execution. M/V Abigail Claire was the base of operations for this project. Our support team included CEMC, Supreme Services, Blanchard Contractors, and Aries Marine.
.png?width=400&name=mn37n5cM%20(1).png)
VERMILLION 214A
2-inch RTJ flange and ball valve installed on bottom of pig trap.
50 bbl MPT tank set on deck to collect flowback.
2-inch hose with Fig. 206 hammer union connections connected pig trap to MPT tank.
25 bbl cut box to collect paraffin.
2-inch hot tap installed on riser.
This is not a requirement. PipeRenew® can be injected into the pipeline from any sufficient entry point on the platform.
VERMILLION 214C
2-inch RTJ flange and ball valve installed on bottom of pig launcher.
50 bbl MPT tank to provide volume for flushing.
2-inch hose with Fig. 206 hammer union connections connected pig launcher to cut box.
25 bbl cut box to collect displaced production fluid.
Skillets installed on top of pig launcher.
2-inch hot tap installed on riser.
This is not a requirement. PipeRenew® can be injected into the pipeline from any sufficient entry point on the platform.
M/V ABIGAIL CLAIRE
3 - 500 bbl tanks to collect solids and flushed liquids.
PE-5 pump to inject PipeRenew®.
3-inch air diaphragm pump for mixing.
3-inch air diaphragm pump to prime PES.
350-gallon mixing tote.
2 - 550-gallon totes for product storage.
50 bbl sea water clean out tank.
PROJECT CHRONOLOGY
Day 1 |
|
|
|
|
|
|
|
|
|
|
|
|
|
|
|
HIGH PERFORMANCE RESULTS
A total of 133 bbl of PipeRenew® treatment was pumped into the line. Approximately 15% of the solution was collected with the production fluid during the displacement and pumping process. Total capacity of the line was only 397 bbl, indicating the line contained 284 bbl of paraffin solids and sludge. This was consistent with the amount collected during the treatment process. Ideal executed the job safely and on schedule, and after seven days, full communication was established.
For more information about how non-hazardous, environmentally
responsible PipeRenew® remediation treatment can cost-effectively
remove paraffin and asphaltenes from your pipeline,
contact your Ideal Energy Solutions representative today.